This summer a revolutionary new aircraft concept took off on its maiden flight: the Flying-V. This concept, which was originally an idea of TU Berlin student Justus Benand during his thesis project at Airbus Hamburg, has been taken a step further by Dr. Roelof Vos and his team at TU Delft. They designed, built and flew a first scale model. The design team used the ParaPy platform from day one to establish a parametric, rule-based geometry of the aircraft and to couple their engineering analysis capabilities. We interviewed Dr. Vos about designing the Flying-V and how ParaPy impacted that process.
How does the Flying-V set itself apart from other tailless aircraft concepts?
The Flying-V can be stretched or shrunk by exchanging constant-cross section parts of the wing. This allows a family concept. Also, the Flying V features a pressurized fuselage consisting of a piece-wise circular-arc cross section. We termed this the “oval fuselage”. A trapezoidal substructure supports these circular arcs and also doubles as the passenger floor and ceiling. This allows for the Flying-V to be pressurized without the introduction of out-of-plane stresses. Therefore, an efficient structure can be synthesized.
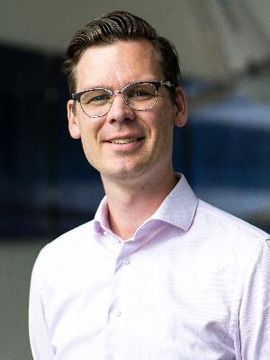
What were the initial challenges you faced in the conceptual design process?
The first challenge was related to coming up with a geometry that would meet three major requirements:
- Fit the passenger cabin, cargo hold and fuel;
- Allow for a structure to be synthesized and sized under a given set of loads;
- Be able to optimize for maximal aerodynamic efficiency.
Why did you choose the ParaPy software?
ParaPy allows for a well-described geometry that can be scripted in rules. Therefore, we were able to program, for example, the oval fuselage shape and parameterize that into the design. By subsequently coupling the parameterized geometry to an optimization algorithm and structural and aerodynamic analysis tools, it allowed us to explore the design space and find a good compromise in the design.
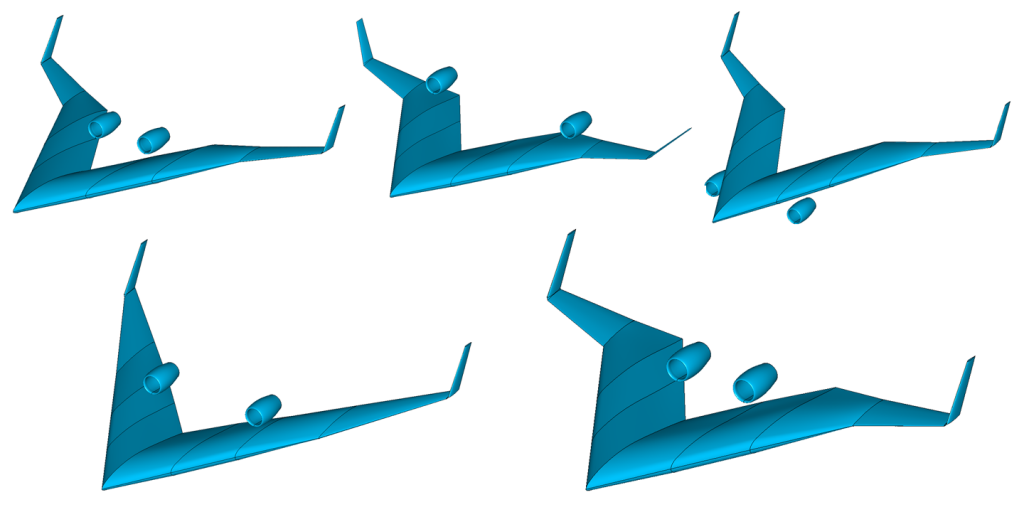
How does your Flying-V app work?
The app can be used in two ways, either through ParaPy’s desktop GUI or with a custom input file. The desktop GUI, which is available out-of-the-box, enables the user to interact with the programmed parametric model, for example to adjust input parameters and directly see the updated geometry or to configure and start disciplinary analyses.
Using the second approach, an input file can be written to list top-level input parameters. This can be done by the developer (i.e. student), the chief designer (i.e. myself), or by an optimizer. Inside the app, knowledge rules are subsequently employed to build up the geometry of the Flying-V. Capability modules, such as the meshing toolbox, are applied to prepare the geometry for disciplinary analysis. ParaPy’s dedicated simulation toolboxes are used to perform these analyses with well-known solvers, such as Nastran for structures, and SU2 and AVL for the aerodynamics.
How many design options were analyzed using ParaPy?
The structural design was the hardest to complete in terms of geometry description. Once a parametric description of the structure was present, sizing the structure for a given load case went relatively fast. We performed between 15 and 25 iterations to size the structure of the Flying-V, where ParaPy was coupled to a sizing algorithm and a linear FEM (Finite-Element Method) solver. For the aerodynamic design we performed 100 iterations, where the ParaPy model was coupled to an aerodynamic solver as well as an optimization algorithm. For the engine positioning study we approached the problem through a sampling method, where we sampled a bounded design space and investigated 50 different engine positions using a two-step approach to refine the search area.

How did ParaPy help with the trade-off between different Flying-V designs?
ParaPy helped by offering the ability to define a parametrized design and its ability to fully automate the coupling with multiple analysis platforms including detailed meshing. This type of automated change in geometry and subsequent analysis was required, for example, in the aerodynamic optimization studies. For every new geometry, ParaPy was employed to make a new grid to feed to the solver. This meant that we were able to scour the design space without having to resort to repetitive work.
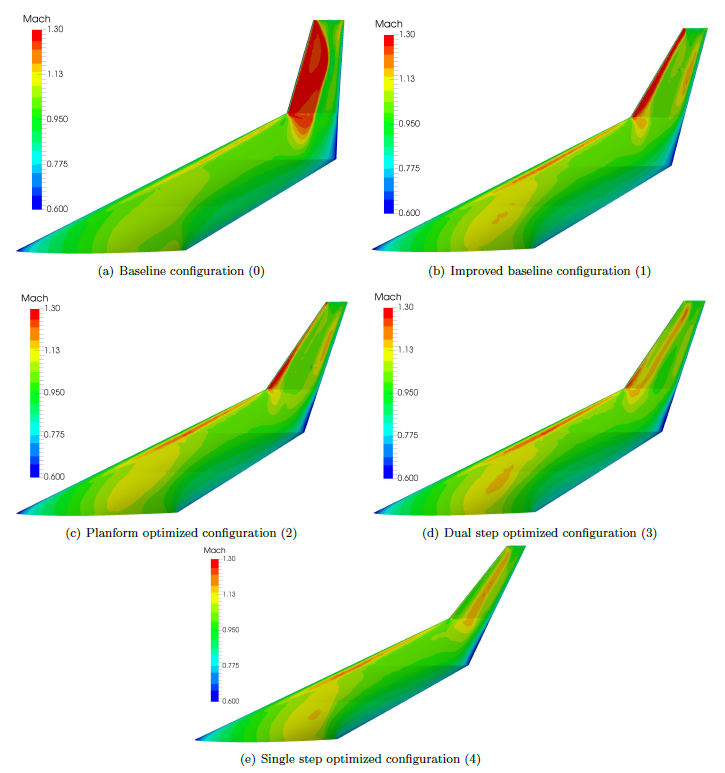
How did you use the toolboxes available in the ParaPy platform?
We used the geometry toolbox to create the parametric design of the Flying-V and took advantage of the ability to extract surface areas and volumes for our payload capacity analysis. We also used the meshing toolbox to mesh the outer surface for aerodynamic analysis as well as for the meshing of the structural elements for the FEM analysis. These meshes were combined with the respective solvers using the aerodynamic (AVL, SU2) and structural toolboxes (Nastran).
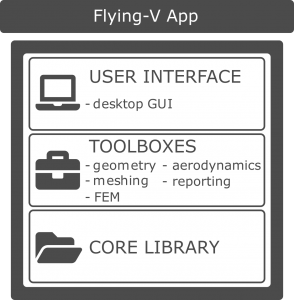
How did ParaPy impact the design process of this innovative concept?
All the innovations in the design came from the people that implemented the design rules into ParaPy. ParaPy was an important asset in demonstrating that the benefits of the Flying-V (i.e. lower weight and higher aerodynamic efficiency) could indeed be achieved with a geometry that could also comfortably support the passenger cabin as well as the cargo hold and the fuel tanks.
How much reduction in weight and drag was achieved in comparison to the baseline design?
The aerodynamic efficiency of Flying-V was 25% higher than that of the reference model. However, the Flying-V was optimized while the reference model was not. Therefore, we scaled that back to 15%. We also computed a 17% reduction in “structural FEM weight” compared to a baseline tube-and-wing aircraft that was sized to the same load case. An overall aircraft design study was subsequently employed to demonstrate a 20% improvement in payload-range efficiency of the Flying-V over its tube-and-wing competitor.
Congratulations with the maiden flight of the scale model. What kind of applications do you think will aid the designer in the next phases of the design?
The previous Flying-V aircraft was very much an outside-in design. We are currently working on a new version that is more inside-out driven. In other words, manufacturability is our starting point. This gives a somewhat different external shape, and we want to find out what we can get out of that shape from an aerodynamic point of view. Aerodynamic optimization and structural design are therefore (again) at the core of the current research. We will continue to work with ParaPy as our main design tool to connect all our analysis methods.
Do you think our ParaPy platform might also be the right thing for you to build your own design application? Don’t hesitate to contact us to learn more about our platform and services.
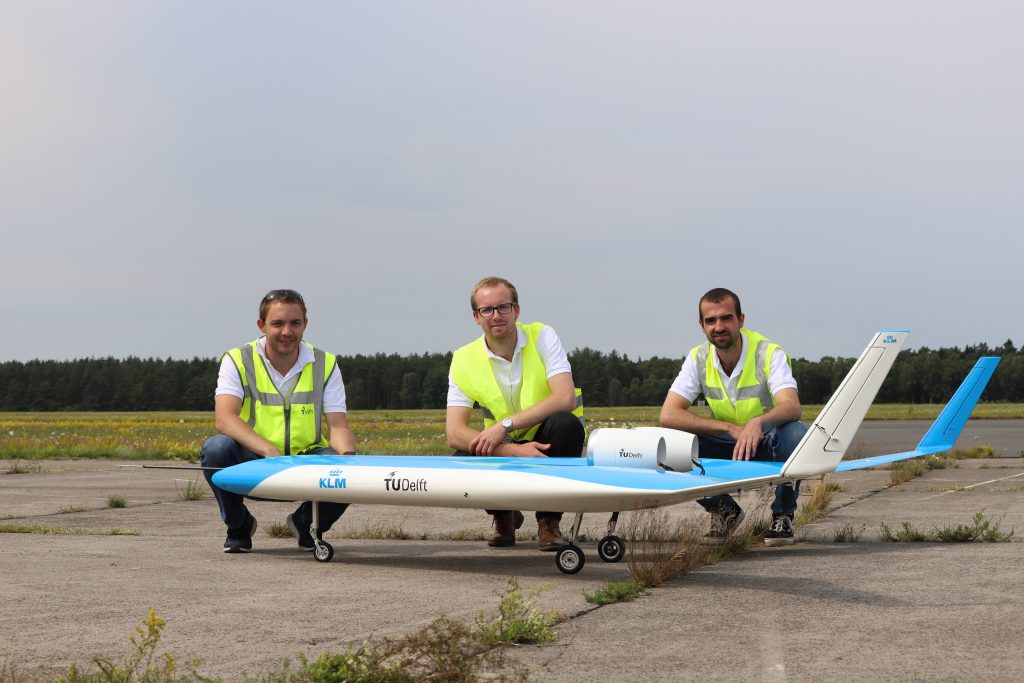
(photo credits: Malcom Brown)
Photo credits: banner and post header by Edwin Wallet